EGC Enterprises Publishes Part Two of a Three Part Series on the Evolution of the EGC Pressure Seal
How EGC Developed a Flexible Graphite Bonnet Seal that Consumes Less Time and Provided Real Cost Savings to Power Plants During Regularly Scheduled Maintenance.
Chardon, OH (PRWEB) May 21, 2012

EGC configures the flexible graphite using valve body and component dimensions, to ensure that the installer is working with a seal of sufficient strength, integrity and mass.
Tested and approved by the Navy in 2003 for use in nuclear powered ships, the EGC Thermafoil flexible graphite pressure seal seemed poised for big things in the general power generation market. In fact, flexible graphite tests performed by electrical power provider, Arizona Public Service (APS), confirmed the Navy’s projected lifespan of a minimum of 26 years for high pressure flexible graphite seals, much longer than the service life of metal seals.
Then, too, flexible graphite speeds and simplifies the seal replacement process. Metallic replacement seals require a very clean surface. If the valve surface is pitted, scratched, out of round or irregular in any way, the metallic ring has little chance of sealing. Flexible graphite, on the other hand, overcomes these irregularities by conforming to the worn valve surface. Where a metal seal has a small clearance between the body ID and the OD of the seal, flexible graphite compresses to fill the entire bonnet cavity, easily conforming and adapting to oversize, out-of-round, steam cut or pitted conditions. It is an insanely forgiving material.
And at the other end of service life, flexible graphite is easy to remove and replace. According to Dick Dudman, an engineer and flexible graphite pioneer at EGC Enterprises, “When you go to replace a worn metal seal, you find that it has bonded itself to the components inside the valve. Major work has to be done to get it out. Some metal seals have to be cut or forced out with hammers, cutting torches and come-a-longs. And the removal process does so much damage that the ID of the valve body has to be reworked and re-machined.
A graphite seal, because it’s so compressible, just doesn’t stick. Says Dudman, “When it’s time to change the seal and you open up the screws, the bonnet will just drop away. You just lift it out the old graphite seal by hand, put the new one in and button the valve right back up again.”
In fact, the ease-of-replacement benefits of flexible graphite seals are so pronounced, they should and probably would have taken the power generation market by storm in 2003 — if not for one, slight problem… they simply took too much time to produce. There was a need for speed.
Dick Dudman remembers it well: “EGC graphite pressure seals required expensive tooling and it took weeks to build. The only business we would get was when the power plant didn’t care what it cost, they just had to have the seal.”
To be of real service to the power generation industry, EGC had to create a way to service the needs of a plant during “outages”, where the plant would shut down once or twice a year, for a few weeks, to do maintenance work. EGC had to develop a quicker and lower cost process to meet this small window of opportunity. This meant . . . no tooling, and thus was born the VSG.
“Through our proprietary process, we configure the flexible graphite, using valve body and bonnet component dimensions, to ensure that the installer is working with a seal of sufficient strength, integrity and proper mass. The VSG pressure seal is a product engineered specifically for their application and it’s all accomplished without expensive tooling,” said Dudman.
Finally, EGC had a seal that could reach power plant service departments in days. Adds Dudman, “Instead of sourcing a new tool for every valve body, our process can make graphite pressure seals from 3” to 24” valves. The VSG is designed to deliver the same safe performance as our original die-molded seals. And, we’re proud to boast a 100% performance rating and ‘zero failure’ track record with ALL of our graphite pressure seals.”
The VSG was introduced in 2008, and has already started to change the way operating plants service their high-pressure line and control valves. Power generation, refinery and pulp & paper customers don’t have to pay tooling costs, and more importantly, receive the product when they need it. Coupled with our new “FastTrac” rapid order program, VSG service is measured in days, not weeks with shipment available in 48 hours or less. VSG . . . On-Time and within Budget.
Corporate Information
EGC is a recognized world leader in engineering and manufacturing of graphite composites for high temperature applications in fluid sealing or thermal systems management.
Ready to talk?
Call us at 440-285-5835, email us, or click below. Together, we can develop a fluid sealing or thermal management solution to meet your explicit needs. And possibly even some you haven’t even realized.
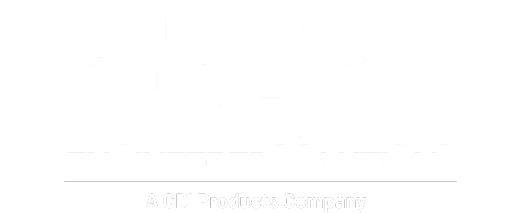
EGC Enterprises Inc.
140 Parker Court
Chardon, OH 44024
Phone 1-800-EGC-0211 (U.S.A. only)
or 440-285-5835
Fax 440-285-8337
Email | egc@egcgraphite.com
Quick Links
© 2021 EGC Enterprises Inc. Privacy Policy | Terms and Conditions | Sitemap