From Cannon Balls to Pressure Seals: Graphite for Sealing
Graphite has qualities that make it a great choice for certain applications in the manufacturing world. Those qualities include its reaction to extreme temperatures as well as its flexibility when engineered a certain way.
In the valve world, flexible graphite provides an ideal choice for many sealing products.
The History of Graphite
The stories about graphite go back to about 1500 when an enormous deposit of graphite was discovered in the Borrowdale Parish in England. One of its first uses was as a refractory material to line molds for cannon balls, which resulted in rounder, smoother ammunition that could be fired farther. This better way of making the balls contributed to the growing superiority of the English Navy back then.
Over the years, graphite’s uses have ranged from writing implements (in Greek, “graphite” means “to write”) such as the Number 2 pencils used for completing tests and schoolwork all the way to lubricants for reducing friction between materials. Recently, graphite has been used in lithium-ion batteries as well as to develop graphene technology, a one-atom-thick cylinder that is 100 times stronger than steel at one-tenth the weight. Graphene is used in semiconductors, to energize batteries and electronics, and to make composites.
Graphite and diamonds are both mineral forms of carbon. Although they are composed of the same element, they have very different structures.
Diamonds are formed in the earth’s mantle under extreme heat and pressure; they are so hard they can cut glass. A diamond’s carbon atoms have a 3D tetrahedral structure.
Graphite is a softer material found in igneous and metamorphic rocks. It forms when carbon is subjected to heat and pressure in the earth’s crust. To produce it, pressures must be about 75,000 psi and temperatures must be about 1,382°F (750°C). Graphite has a 2D layered structure with the carbon atoms arranged in a honeycomb pattern.
Graphite is a mineral of extremes. On one hand, it’s soft and has a very low specific gravity. On the other hand, it is very resistant to heat and is nearly inert when it comes into contact with almost any other material. These properties give it a wide range of uses in manufacturing.
Flexible Graphite
More than half a century ago, Union Carbide Corporation was inspired by the graphite flake to make a product that was “flexible” while maintaining all the characteristics of graphite. The resulting flexible graphite displayed properties of thermal stability and thermal conductivity. It was also naturally lubricious and resistant to most chemicals, yet flexible and compact. It conformed to any cavity while remaining resilient.
Flexible graphite is manufactured from mineral graphite or from expandable flake graphite (image above). It’s prepared by chemically treating natural graphite flake in a way that forms a compound between the layers of its structure. This intercalation (between the layers) is then rapidly heated to decomposition. The end result is an expansion in size by 80-fold over the raw material. The expansion (also called exfoliation) produces a worm-like (vermiform) structure with a highly active, arborescent, rough surface (image to the left). At this point, the worms are calendared into a sheet form (image below). This calendaring involves only mechanical interlocking of the expanded flakes―no binders are required. In fact, all the chemicals added to the flake to promote expansion are removed during this high-temperature process. The resulting sheet product is essentially pure graphite containing a minimum of 98% elemental carbon by weight. It has been created in a controlled process and has a highly aligned structure.
Premium sheet products (such as those required for nuclear service) are specially processed and have extremely low levels of potential impurities (typically 99.9% carbon). Corrosion and oxidation resistance can be added as an integral part of the sheet material.
Flexible graphite sheets can be laminated together with an adhesive or thermal bond. The result is increased thickness of the laminate for a gasket or ring. Laminates can be thermally treated to decrease outgassing for use in high-temperature applications when small quantities of volatiles from outgassing of the adhesive could promote contamination.
Materials also can be laminated with metallic and nonmetallic materials to improve handling, blowout resistance and mechanical strength. Laminating materials that are dissimilar can alter the physical, thermal, chemical, and electrical properties of the flexible graphite.
Engineered sealing products can be fabricated from flexible graphite sheet and roll stock. For example, corrugated tape can be slit from rolled sheet, then crinkled for use in valve stem or pump packings. Tape is also the raw material used for making-die molded rings for valve and pump packings. Adhesive-backed material can be made for fabricating form-in-place gasket tapes or flat thread sealant tape as well.
Attractive Qualities
Homogeneous flexible graphite sheets are used for a wider range of temperature conditions than any other sealing material. Cases of using this material exist for temperatures as low as -400°F (-240°C) and as high as 5400°F (3000°C).
Flexible graphite can oxidize when exposed to air or other gasses, causing weight losses. In oxidizing atmospheres, oxidation of flexible graphite can begin at 975°F (525°C). However, thin-edged exposure of packings and gaskets has successfully withstood extended periods of air and process fluid temperatures of up to 1500°F (815°C).
Beyond temperature, flexible graphite offers softness and resiliency which contribute to its ability to micro-seal a surface. When built to the proper thickness, the material also adjusts for out-of-flatness conditions and can absorb imperfections but still have enough friction on the mating surfaces to remain in position. One example of where we see this occurring is in pressure seals.
Pressure seals are critical in power generation, pulp and paper, refineries, and chemical industries which all have minimum operating pressures of 500 psi.
The pressure seal is a valve design that uses the valve system pressure to provide sufficient force against the valve body, body inside diameter, and the bonnet surfaces. As system pressure increases, so does the force on the pressure seal gasket.
A seal gasket made of metal pressure conforms to the inside diameter of the valve. Although most of the gasket is built for structure, the working point is the “toe.” When the system is activated, the toe forms a seal that can keep thousands of pounds of pressure and system media contained in the valve.
Typically a metal pressure seal is made of malleable iron and sometimes coated with silver to help with conformance. The seal is placed just below the keeper ring, and when enough force is applied, the metal will move into its correct position and force the toe between the body inner diameter and the bonnet surface. This seal becomes a permanent part of the valve until it has to be replaced.
Cycling can have a severe effect on a metal pressure seal. Two types of cycling occur: thermo-cycling, a process whereby the temperature raises or lowers, and pressure-cycling, whereby operators turn the system on or off. When a system goes off, the metal seal starts to contract. When pressurized again, the seal wants to expand. When both types of cycling occur at the same time, the metal seal will weld itself into position.
An Alternative
An alternative to the metal pressure seal is a seal made of flexible graphite. Such seals often are a retrofit for metal seals used in the aftermarket. In some cases, they are used as OEM pressure seals.
Structurally, flexible graphite far exceeds the temperature and pressure requirements that accompany pressure seal applications. The flexible graphite is capped with metal above and on the toe, and it will not oxidize in steam service. Cycling has no effect on the flexible graphite pressure seal. This is because as the system turns on or off, and regardless of temperature extremes, flexible graphite springs back. Its non-stick surface also makes the pressure seal as easy to remove as it is to install. Unlike a metal seal, no re-machining of the valve surface after removal is done. In fact, flexible graphite hides most imperfections left when replacing a metal seal.
Some call graphite the crazy mineral that ranks just above anthracite coal and just below a diamond. Regardless of what it’s called, however, the properties that result when flexible graphite is made make this material a good choice for fluid sealing applications.
Ready to talk?
Call us at 440-285-5835, email us, or click below. Together, we can develop a fluid sealing or thermal management solution to meet your explicit needs. And possibly even some you haven’t even realized.
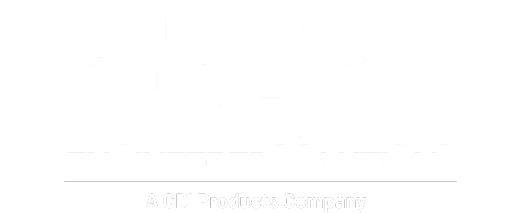
EGC Enterprises Inc.
140 Parker Court
Chardon, OH 44024
Phone 1-800-EGC-0211 (U.S.A. only)
or 440-285-5835
Fax 440-285-8337
Email | egc@egcgraphite.com
Quick Links
© 2021 EGC Enterprises Inc. Privacy Policy | Terms and Conditions | Sitemap